Forged
Products
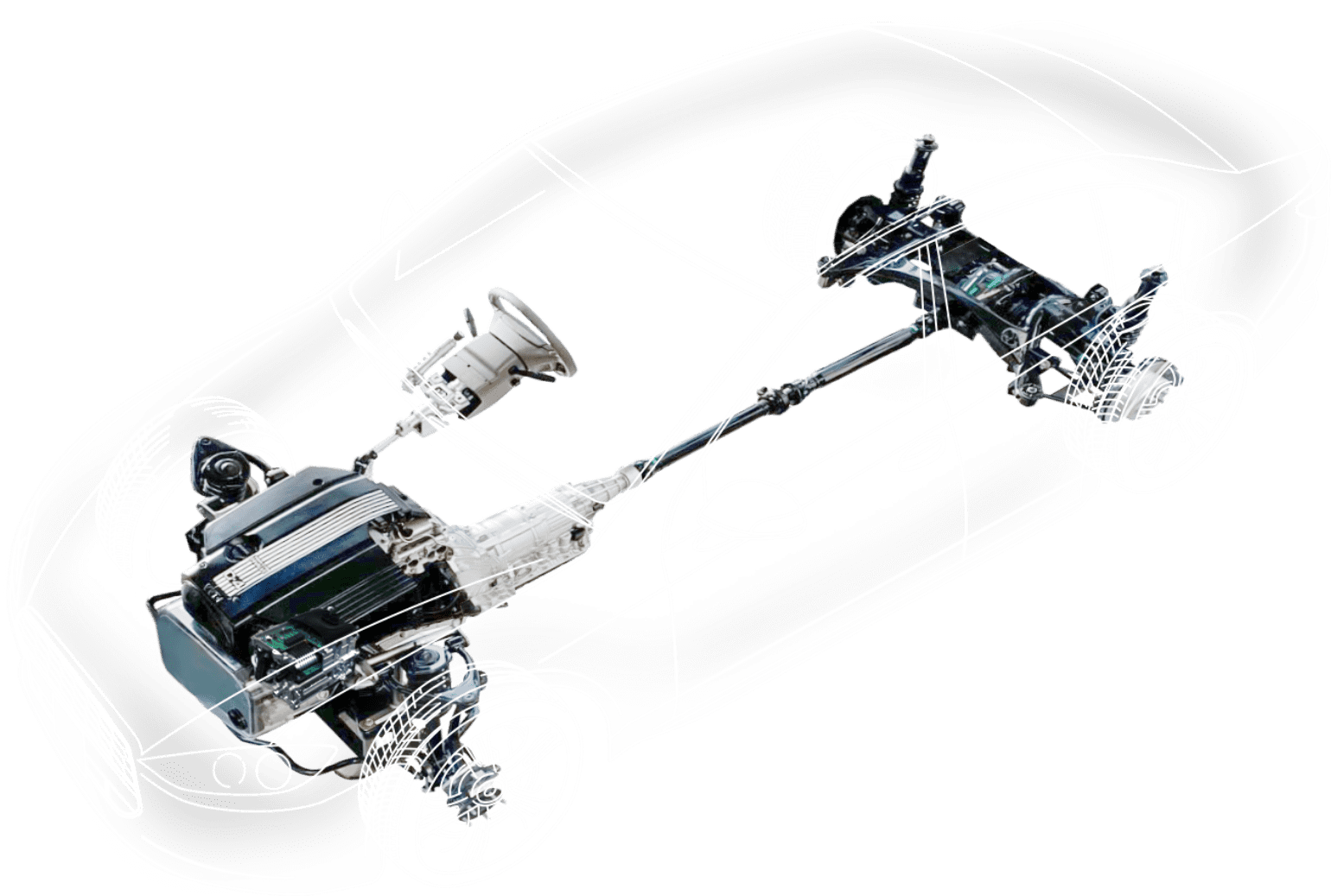
-
e-Axle Unit Products (for BEVs)
-
Engine Products
-
Transmission Products
-
Driveline Products
-
Chassis Products
e-Axle Unit Products
The unit parts of the BEV Traction Motor System for which demand is expected to surge.
We contribute to customer needs and CN by developing both steel materials and forging methods.
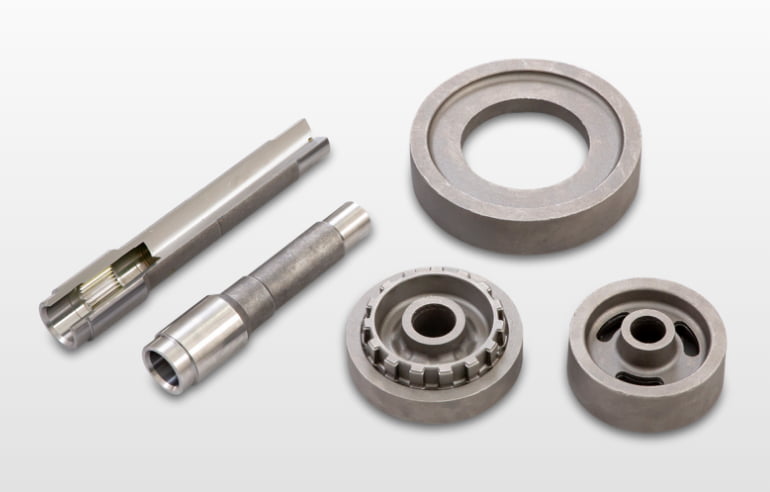
Output Shaft
Process | Cold Forging + Machining |
---|---|
Weight | Up to 3 kg |
Features | Cold forging and machining processes, which have been common in the past to separate production lines, will be combined into one, and customer’s machining processes will also be actively incorporated to realize inexpensive, high-value-added manufacturing. |
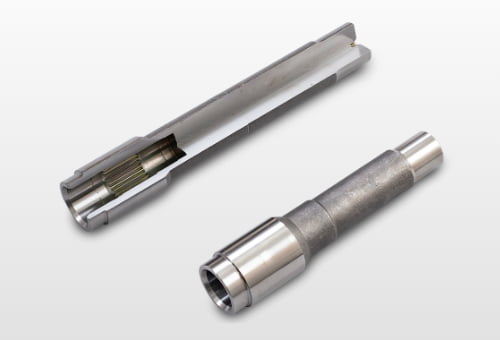
Counter Driven Gear
Process | Hot Forging + Cold Forging |
---|---|
Weight | Up to 7 kg |
Features | A partial cold forging method is applied to hot forgings for higher precision. This method greatly reduces or eliminates the customer's machining process, resulting in significant cost reductions. |
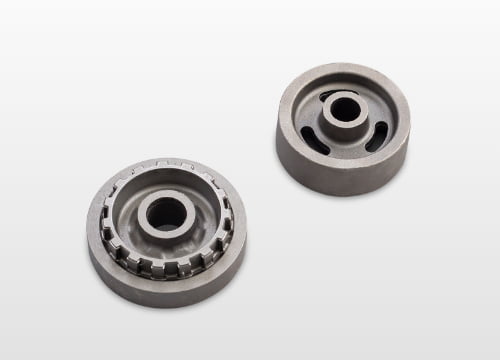
Differential Ring Gear
Process | Hot Rolling Mill |
---|---|
Weight | From 2 kg to 6 kg |
Features | The hot rolling mill method, which enlarges ring-shaped hot forgings at high temperatures, is the most suitable method for manufacturing differential ring gears. We provide low-cost, environmentally-friendly products with industry-leading high yields and energy-saving technologies. |
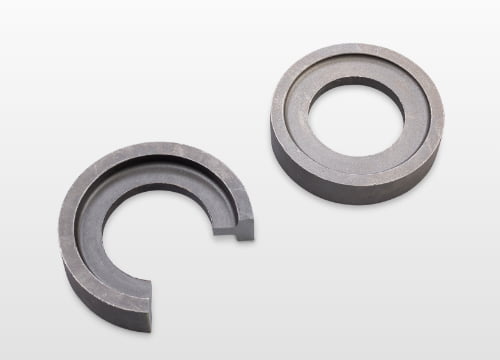
Engine Products
Main drive unit parts for automobiles.
We contribute to higher quality and lower costs with technologies developed over many years.
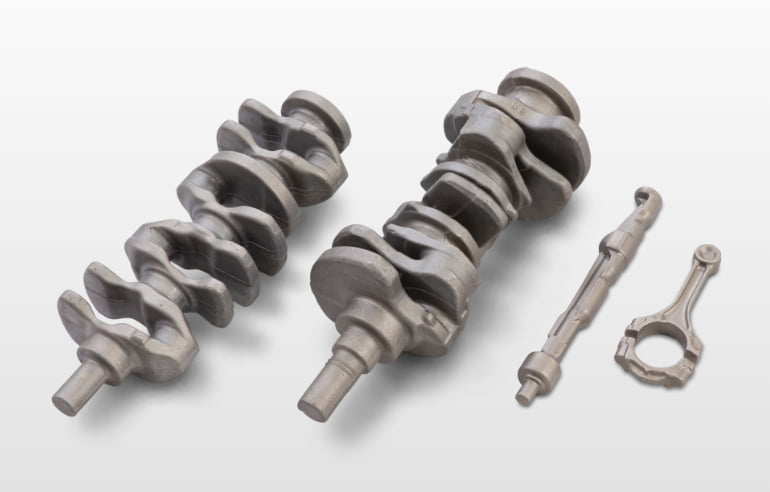
Crankshaft
Process | Hot Forging |
---|---|
Weight | Up to 46 kg |
Features | Our twist and coining technology provides high-precision and highly balanced products and meets the diverse product specifications of our customers. |
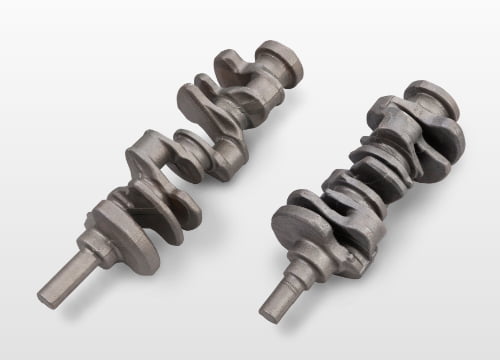
Crankshaft for Small Serial 3-Cylinder Internal Combustion Engine
Process | Hot Forging |
---|---|
Weight | Up to 10 kg |
Features | We developed a method of forming two small crankshafts that are connected together and then splitting them in a later process to achieve high productivity and resource conservation. We provide high-quality products at low cost. |
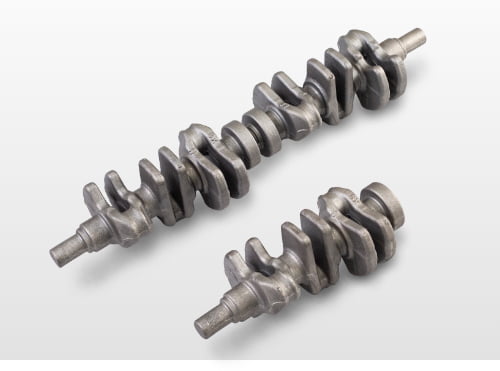
Connecting Rod and Cap
Process | Hot Forging |
---|---|
Weight | Up to 2 kg |
Features | We provide high-quality products at a low cost in response to customer requests, using the near-net-shape technology we have developed over many years. We also propose steel products for further functional enhancement. |
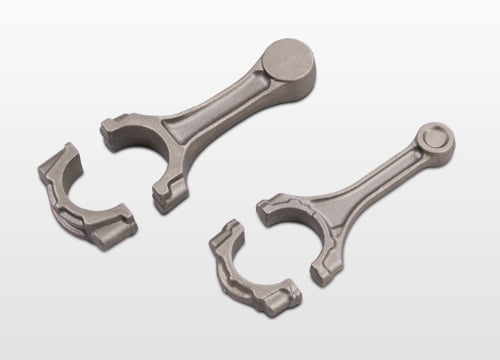
Transmission Products
Shift and drive transmission parts that require reliability.
By choosing and combining the optimum forging methods according to the product specifications, we can achieve unprecedented high functionality.
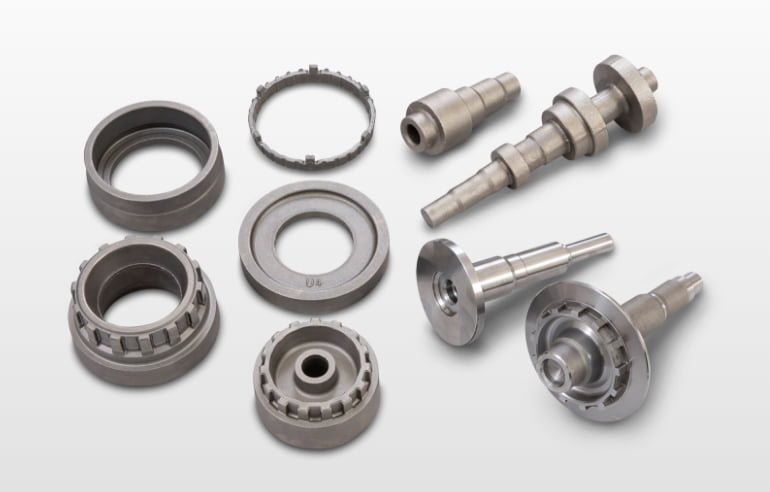
CVT Primary Shaft Parts
Process | Hot Forging + Machining + Cold Forging |
---|---|
Weight | Up to 5.5 kg |
Features | Cold forging technology for high-precision inner splines that are difficult to machine was developed to achieve drastic reductions in machining time and cost reductions. |
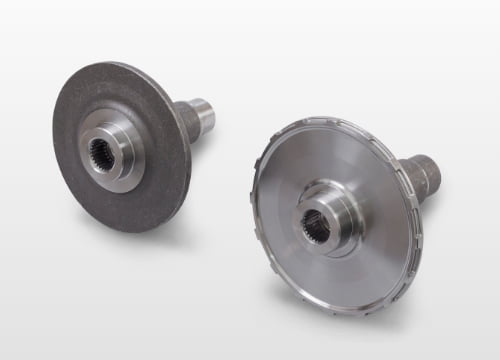
CVT Secondary Shaft Parts
Process | Hot Forging + Machining + Cold Forging |
---|---|
Weight | Up to 7 kg |
Features | Partial cold forging is applied to hot forged parts with long shafts, eliminating machining of parking lock gears. This greatly reduces or eliminates the customer's finishing machining processes, resulting in significant cost reductions. |
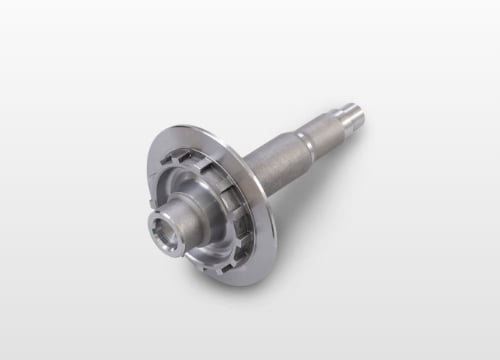
Drive Pinion
Process | Warm Forging |
---|---|
Weight | Up to 3 kg |
Features | We developed a warm forging technology that can be used to forge parts at lower temperatures than hot forging. Warm forging enables near-net-shaping of the entire product as well as deep holes, greatly reducing the customer's finish machining processes. We also contribute to the reduction of CO2 emissions due to lower temperature forging. |
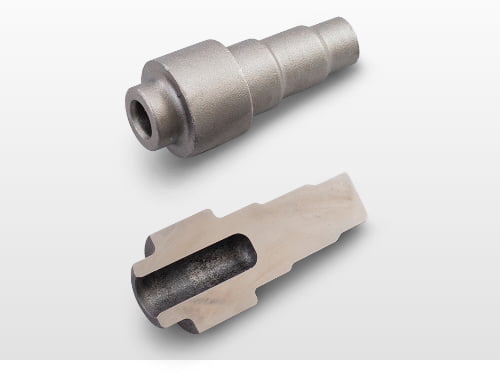
Counter Driven and Drive Gear Parts
Process | Hot Forging + Cold Forging + Machining |
---|---|
Weight | Up to 7 kg |
Features | Partial cold forging is applied to hot forged parts, eliminating machining of parking lock gears. This greatly reduces or eliminates the customer's finishing machining process, resulting in significant cost reductions. |
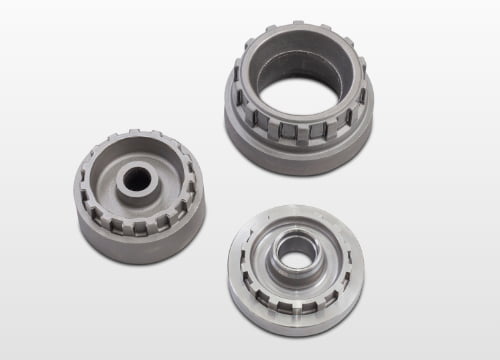
Differential Ring Gear Parts
Process | Hot Rolling Mill + Machining |
---|---|
Weight | From 2 kg to 6 kg |
Features | The hot rolling mill method, which enlarges ring-shaped hot forgings at high temperatures, is the most suitable method for manufacturing differential ring gears. We provide low-cost, environmentally-friendly products with industry-leading high yields and energy-saving technologies. |
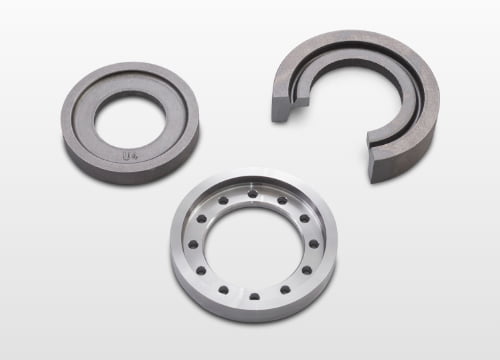
Planetary Ring Gear and Other Ring-Shaped Parts
Process | Hot Forging + Cold Rolling Mill, Hot Rolling Mill |
---|---|
Weight | From 1 kg to 4 kg |
Features | In addition to the hot rolling mill method, we also use the cold rolling mill method, which enlarges ring-shaped hot forgings at room temperature, and we propose this technique based on the parts specifications. We provide low-cost, environmentally friendly products with industry-leading high yields and energy-saving technologies. |
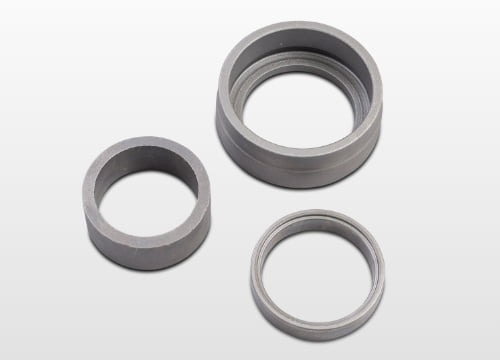
Output Shaft Parts
Process | Hot Forging + Machining + Cold Forging |
---|---|
weight | Up to 3 kg |
Features | Cold forging technology for high-precision inner splines that are difficult to machine was developed to achieve drastic reductions in machining time and cost reductions. |
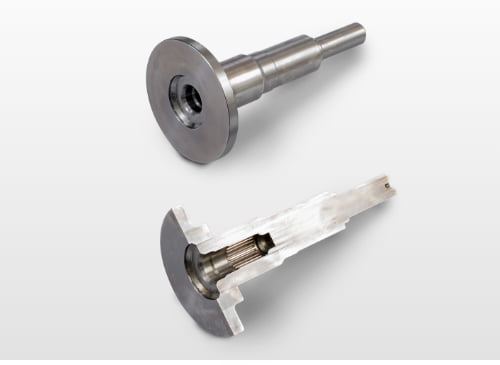
Driveline Products
Drive transmission parts that require reliability.
We provide customers reliable products through our advanced forging technologies and a thorough quality assurance system.
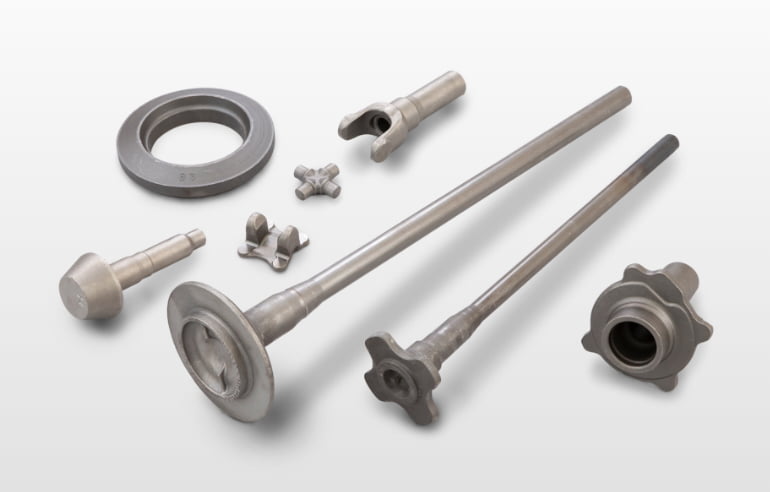
Differential Ring Gear
Process | Hot Rolling Mill |
---|---|
Weight | From 2 kg to 7 kg |
Features | The hot rolling mill method, which enlarges ring-shaped hot forgings at high temperatures, is the most suitable method for manufacturing differential ring gears. We provide low-cost, environmentally-friendly products with industry-leading high yields and energy-saving technologies. |
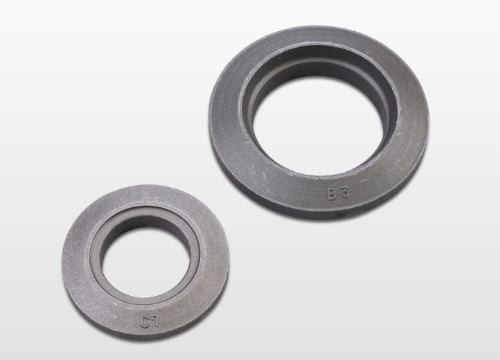
Drive Pinion
Process | Warm Forging, Hot Forging |
---|---|
Weight | From 1.8 kg to 5 kg |
Features | We developed a warm forging technology that can forge parts at lower temperatures than hot forging. Warm forging enables production of near-net-shapes of entire products as well as multistage axles and greatly reduces the customer's finish machining processing. We also contribute to the reduction of CO2 emissions due to lower temperature forging. |
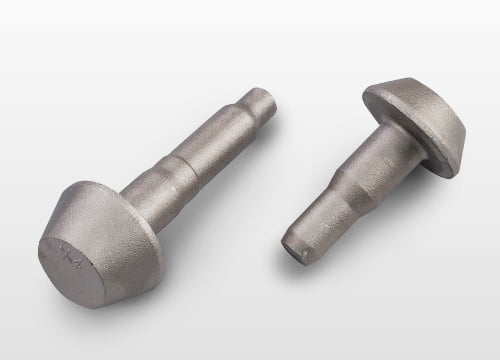
Axle Shaft Parts
Process | Hot Forging + Cold Forging |
---|---|
Weight | From 4 kg to 12 kg |
Features | The flange part (round shaped or cross shaped) at the end of the shaft is hot forged, and the shaft part is cold forged (extrusion method) after hot forging to achieve high yields. Since the dimensions of the shaft after cold forging are highly precise, the customer can perform machining-less finishing. |
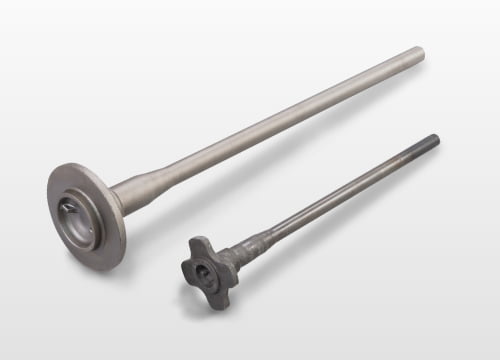
Sleeve Yoke Parts
Process | Hot Forging |
---|---|
Weight | From 1 kg to 3.3 kg |
Features | We achieved high-precision hollowing of long-axis parts with irregular shapes. Significant near-net-shaping is possible, which greatly reduces finish machining by the customer. |
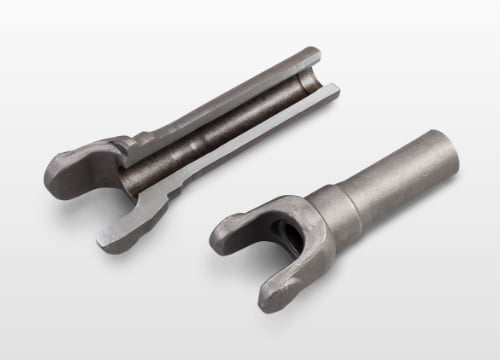
Flange Yoke Parts
Process | Hot Forging + Cold Forging |
---|---|
Weight | From 0.5 kg to 1 kg |
Features | A partial cold forging method is applied to hot forgings for significant near-net-shaping. We make the parts compact and greatly reduce the customer's finish machining processes. |
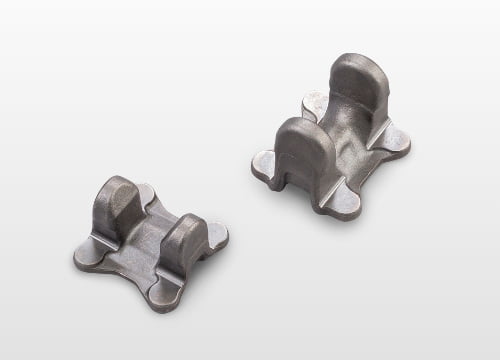
Chassis Products
Important components that greatly affect the comfort and safety, such as driving stability and braking performance, of automobiles.
We provide customers reliable products through our advanced forging technologies and a thorough quality assurance system.
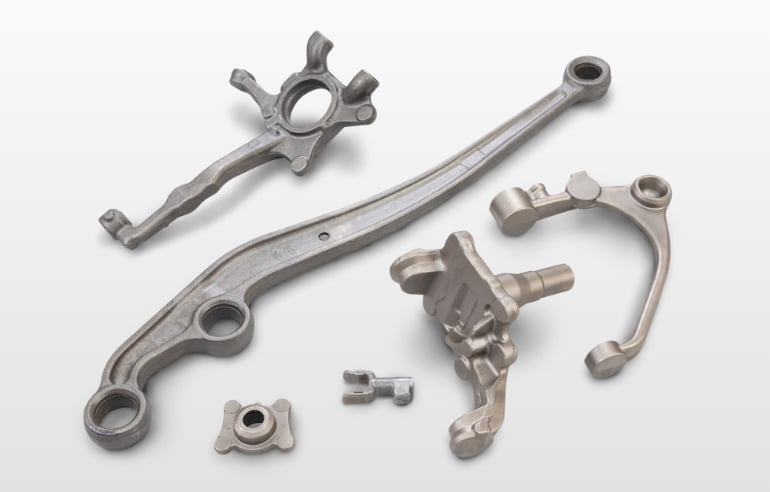
Steering Knuckles
Process | Hot Forging |
---|---|
Weight | Up to 17 kg |
Features | We meet customer demands with our advanced forging technology and contribute to automobile safety and comfort through a thorough quality assurance system. |
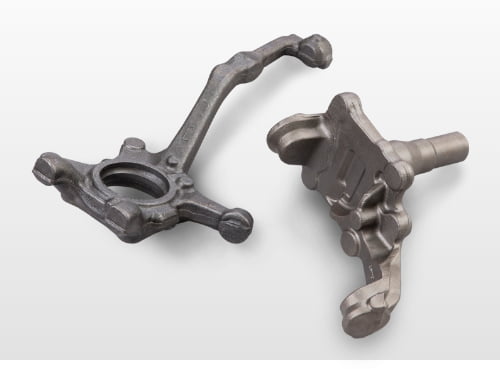
Leading Arm
Process | Hot Forging + Painting + Machining + Assembling |
---|---|
Weight | Up to 10 kg |
Features | We propose the optimal shape to meet the customer's needs with our forging technology developed over many years. Our thorough quality assurance system contributes to automobile safety and comfort. |
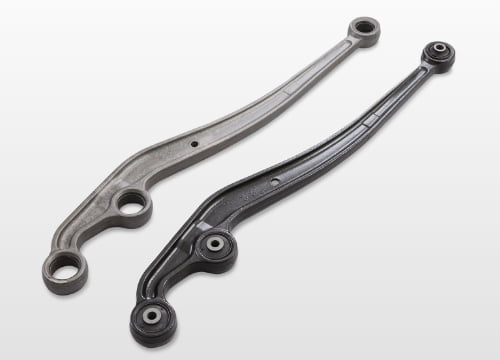
Product
inquiries
Internet
Please complete any inquiries from the below.
- Please understand that we may not be able to accept specific orders depending on the circumstances even for information given on this website. Feel free to contact us for the latest information.
Note that information given on this website is subject to change without notice.