Three strengths/ development cases
Three strengths
01 The world’s strongest bonded magnet
MAGFINE is the world’s strongest Nd anisotropic bonded magnet with magnetic strength five times that of ferrite sintered magnets, twice that of Nd isotropic bonded magnets, and half of Nd sintered magnets.
It is because we use anisotropic magnet particles, which are produced by the d-HDDR method and have excellent magnetic properties.
Since MAGFINE is a composite material made of magnetic particles and resin, it has a high degree of freedom in shape, and we can pursue a motor output that is equal to or greater than that of a Nd sintered magnet that has strong magnetic force in a smaller size by realizing an ideal motor design.
Moreover, since there is a resin between the magnetic powder, it has a feature of being about 100 times more difficult for the current to flow as compared with Nd-sintered magnets.
Since there is almost no flow of eddy currents that occur in the magnets in high-speed rotating motors and the amount of self-heating of the magnets is small in this product, it can suppress the decrease in magnetic force (thermal demagnetization) and improve the motor efficiency.
02 Omission of motor manufacturing process
The cutting machining, assembly bonding, and magnetization processes that are usually required in motor manufacturing can be reduced to a single process through integrated injection molding. As a result, we can reduce the number of employees and facilities, and resolve problems related to production technology such as variations in adhesion and magnetization.
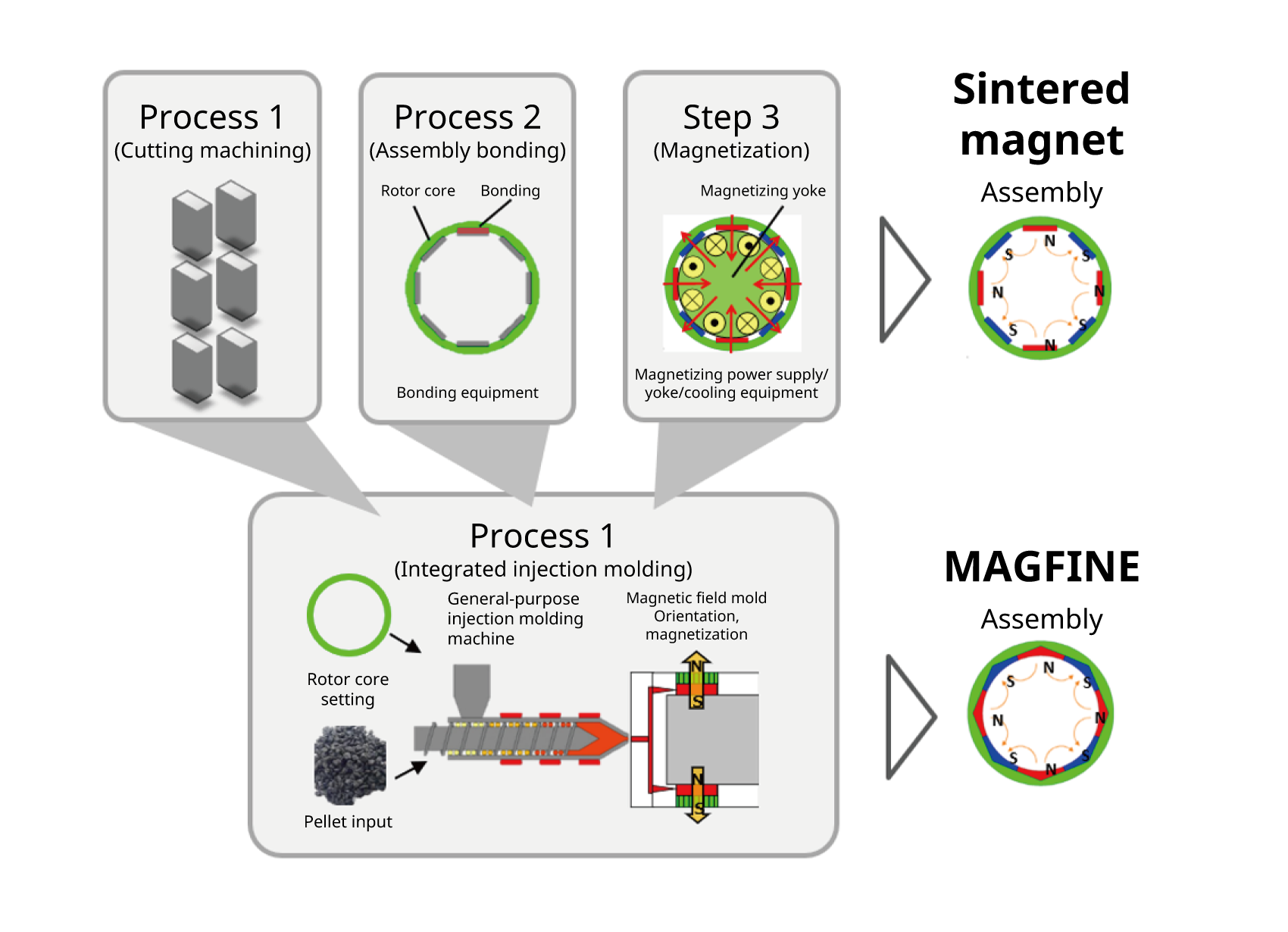
03 Resource saving (Dy-, Tb-, and Co-free)
In addition to Dy and Tb as heavy rare earth metal, which are precious earth resources and whose supply amount is unstable and prices fluctuate greatly, Co that is a specified chemical substance is not used at all. Therefore, resource risks can be mitigated, and stable procurement of resources can be expected.
Story1 Design of IPM rotor using MAGFINE free of Dy and Tb as heavy rare earth metal
Challenge
Heavy rare earth metal (Dy, Tb) contained in Nd-sintered magnets used in high-efficiency motors with the IPM structure for air conditioner compressors and in-vehicle motors pose a high resource procurement risk.
Outcome
Resource procurement risk is mitigated by designing the IPM rotor using anisotropic bonded magnets (MAGFINE) free of heavy rare earth metal (Dy, Tb).
Case details
In general, high-efficiency motors with the IPM structure using Nd sintered magnets are used for air conditioner compressors and in-vehicle motors. Such motors increase torque with the creation of an IPM (Interior Permanent Magnet) structure that effectively utilizes reluctance torque in addition to magnet torque by embedding Nd-sintered magnets inside the rotor.
However, the plate-like shape of Nd-sintered magnets has the highest cost advantage, and thus the IPM was also designed on that extension, and there was limitation to the use of reluctance torque.
On the other hand, the anisotropic bonded magnet MAGFINE developed by our company did not contain any heavy rare earth elements such as Dy and Tb, and therefore it could mitigate resource procurement risks, but it was necessary to devise a rotor design in order to produce the same output in the same size because its magnetic force was half that of Nd-sintered magnets. As a design point, in order to compensate for the lack of magnetic force, we decided to design it by making use of the degree of freedom in shape that was the advantage of the bond magnet for items related to equations (1) to (4) on the torque as shown below.
Example of analysis
With respect to the current model composed of Nd-sintered magnets, we examined MAGFINE with the models as shown below.
The relationship between the number of poles and the reluctance torque (Lq-Ld) and the relationship between the number of poles and the magnet weight are shown below.
As a result, we were able to reduce the amount of Dy used to 0 g with the same torque performance as shown below, and thereby reduce the rare earth resource index* by 33.5 points as compared with Nd-sintered magnets.
- Rare earth resource index: As of November 2011, Nd was $290/kg and Dy was $2877/kg, and therefore the index was defined as the amount of Nd used + 10 x the amount of Dy used. In other words, a Nd-sintered magnet is 26 + 10 x 5 = 76, and MAGFINE is 42.5 + 10 x 0 = 42.5.
Current model Nd sintering |
Model4 MAGFINE |
|
---|---|---|
Amount of magnet used (g) | 100 | 137 |
Nd(g) | 26 | 42.5 |
Dy(g) | 5 | 0 |
Rare earth resource index Nd∔10Dy |
76 | 42.5 (44% reduced) |
- Calculated based on market prices, etc. as of 2011.
Story2 Design of outer rotor that realizes 30% weight reduction of the motor
Challenge
Reduction of the weight of the motor to enable the drone to fly for a long time.
Outcome
Approximately 30% weight reduction was achieved as compared with conventional rotors for drones.
Case details
In general, a need for motors for drones is to reduce the weight of the motors so that drones can fly for a long time. However, it is necessary to ensure a certain motor output in order to secure the payload (loading weight). The weight and output of a motor are in a trade-off relationship in terms of a design concept, and increasing the output increases the weight proportionally, and therefore the output density (output/weight) is used as a measure of weight reduction.
In conventional motor design, design was performed for increasing the rotation torque by bonding multiple magnets to an iron housing with high magnetic properties and connecting the magnetic flux lines of adjacent magnets through the housing to improve the generated magnetic field in order to ensure the output. However, since the housing was made of iron having a high specific gravity, there was a limitation to weight reduction (Figures 2a and 2b).
Therefore, we aimed to greatly reduce the amount of yoke used and improve the output density of the motor by applying the previously developed “Integrated injection molding technology” (Figure 1) and using a light, non-magnetic magnesium alloy for the housing, conducting Integrated injection molding of MAGFINE as the bonded magnet after placing a yoke with the minimum thickness necessary to connect the magnetic flux lines on the inner diameter side of the housing, and making the magnetic pattern of the magnet polarly anisotropic orientation. (Fig. 3, Photo 1).
Figure 1 Integrated injection molding technology
Figure 2 Structure of rotor assembly
Photo 1 Rotor assembly
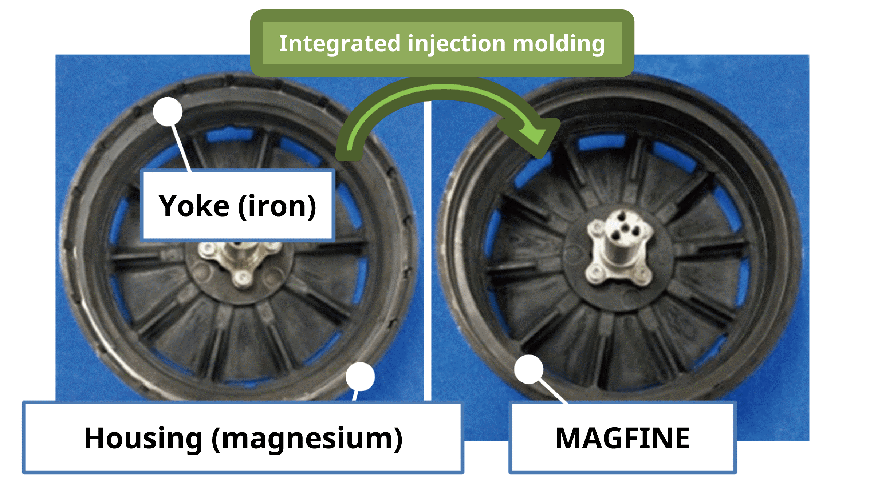
Figure 3 shows the characteristics of the developed motor and another company’s motor. As compared with other companies’ motors, this motor had approximately double the maximum output and is approximately 30% lighter, resulting in a 3.5-fold improvement in output density (output/weight) and a significant weight reduction. Currently, this developed motor is employed for pesticide spraying drones (pesticide payload of 12L and a long flight for a maximum flight time of 180 minutes).
Outer rotor type brushless driver