愛知製鋼の鍛造品生産量は年間約27万トン。
そのうち半数以上を占めている主力製品が、リングギヤを含む駆動部品である。
当社は、創業以来「よきクルマは、よきハガネから。」という精神の下、
幾多の駆動部品用鋼の開発を成し遂げてきた。
ただ、言葉では「成し遂げてきた」と簡単に言えるものの、
実際は一つの新鋼種を開発するだけでも何年もかかる大仕事である。
何年もかけて
たくさんのハードルを一つ一つ乗り越えたものだけが
ようやく新しい開発鋼として誕生するのだ。
近年、自動車産業のグローバル化の一環として2000年代に海外での現地調達化が進み、顧客のニーズが現地メーカーでも生産できる鋼にシフトしたことから、性能は優れていても、日本でしか生産できない新鋼種の開発が停滞してしまった。もちろんその流れは当社にも押し寄せ、新鋼種の量産化ができない期間がしばらく続いた。
その停滞を打ち破ったのが「マイルド浸炭用鋼(MSB20)」の開発だ。
まず、「マイルド浸炭」と聞いても、関係者以外はピンとこないのが正直なところであろう。リングギヤなどの駆動部品を製造する際には、使用時の損傷を防ぐため、素材の表面に炭素を浸み込ませ、焼入れ、焼き戻しを行って、表層を硬化させる必要があるが、この炭素を浸み込ませるプロセスを「浸炭」という。
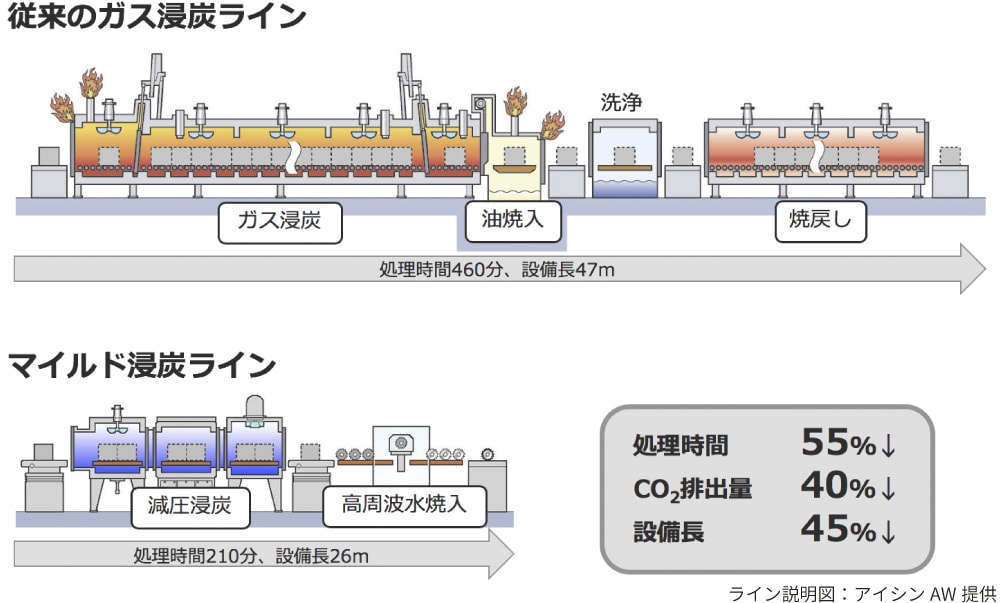
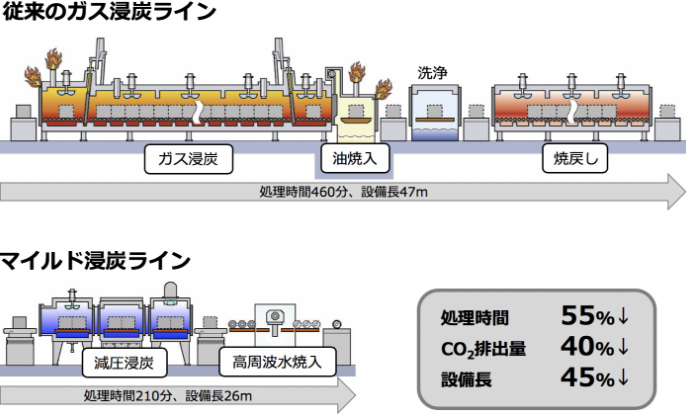
主流の浸炭方法であるガス浸炭は、時間がかかる上、環境への負荷が大きいため、アイシン・エィ・ダブリュ(AW)は、2006年に「マイルド浸炭プロセス」を完成させた。このプロセスは、従来の方法に対し、大幅な浸炭時間の短縮(軽浸炭という意味でのマイルド)とCO2排出削減(環境にマイルド)を実現したものである。さらに、高強度・低歪みという付加価値も併せ持っている。
そして、マイルド浸炭プロセスの完成から2年後の2008年、AWから「マイルド浸炭プロセスを活用した省資源鋼の開発」という要請を受けたのが、今回の鋼種開発の始まりであった。
高強度かつ省資源の鋼は従来では考えられなかったが、AWと協力し、マイルド浸炭という特殊なプロセスを最大限活用できるように開発を進めた。その中で、様々な量産品質 課題に直面しながらも、共同開発先のAWや他部署含め、関係者のチームワークで乗り越え、解決策を見出した。
そして、ついに2012年、希少金属であるクロムとモリブデンが全く使われないにもかかわらず、25%も高い強度を持つ「マイルド浸炭用鋼」のリングギヤの量産がスタートした。
現在もその画期的な鋼は生産量を増やしており、AWのトランスミッションの一部として、世界中を駆け巡っている。
この開発をきっかけにCASE時代に対応した駆動部品用鋼の開発の可能性をさらに広げていきたい。
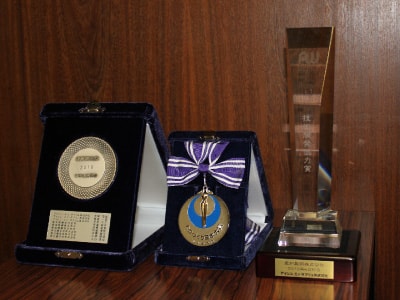
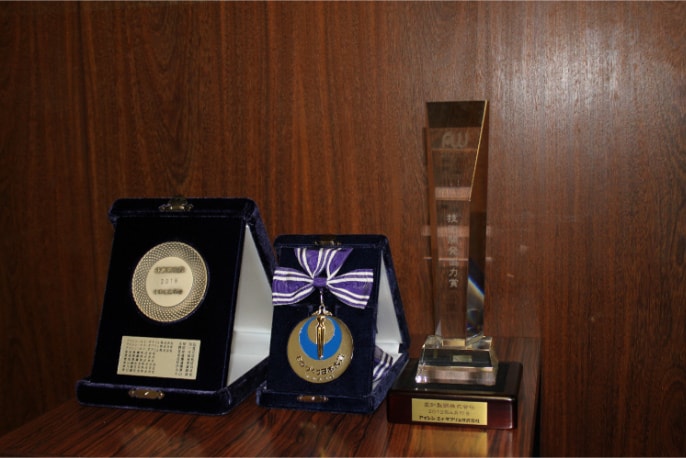
マイルド浸炭用鋼の開発は、
3件の特許登録のほか、
ものづくり日本大賞経済産業大臣賞、
日本金属学会技術開発賞、
アイシンAWの技術開発協力賞など、
業界から高い評価を得た。
社内では社長表彰の最優秀賞を受賞した。