Society
Diversity & Inclusion
Basic approach
Aichi Steel believes that employees with diverse values, abilities, and experiences fulfilling their potential by accepting and learning from each other will lead to the creation of new value. To this end, we are committed to securing and training human resources and improving our in-house environment.
Promoting advancement of women
Aichi Steel is committed to creating an environment in which women can choose flexible workstyles to pursue their goals. We support career development through training and other measures, and have adopted systems to help women balance work and life events. These include the Nice Family System, which is centered on childcare and nursing care support systems, as well as flextime system without a core period and working from home system. We are also focusing on awareness initiatives, such as providing e-learning on childcare support systems to all managers, in order to promote understanding in the workplace and among supervisors and make it easier for employees to take childcare leave regardless of their gender. As a result, in FY2023, the percentage of male employees taking childcare leave increased significantly from the previous year to 69.7%.
FY2022 | FY2023 | ||
---|---|---|---|
Rate (and number) of female managers*1 | 1.0% (4 people) | 1.3% (5 people) | |
Rate (and number) of male employees taking childcare leave*2 | 33.3% (22 people) | 69.7% (53 people) | |
Wage difference between male and female employees*1 *3(%) | All employees | 66.5% | 65.4% |
Full-time employees | 68.2% | 68.2% | |
Part-time/temporary employees | 68.7% | 62.0% |
- Calculated based on the provisions of the "Act on the Promotion of Women's Active Engagement in Professional Life"
- Based on the provisions of the "Ordinance for Enforcement of the Act on Childcare Leave, Caregiver Leave, and Other Measures for the Welfare of Workers Caring for Children or Other Family Members," calculating the percentage of childcare leave, etc. taken under Article 71-4, Item 1.
- There are no gender differences in our pay and evaluation systems, and any wage differences between men and women are due to factors such as length of service, the ratio of men to women in manager positions, and the ratio of men to women in different positions at different pay levels.
Senior employee participation
In view of the declining labor force and the need to maintain and improve on-site capabilities, we believe it is important to maximize the performance of our senior employees (aged 60+). We have established a "Nice Senior System" that allows all those who wish to continue to work from their retirement age until their pension benefits begin. We are improving work environments and reviewing compensation packages while holding discussions with labor and management to ensure that senior employees can continue to work with a sense of security and a high level of motivation. We also conduct initiatives to help senior employees develop self-sustaining careers, including seminars on such topics as "Ways of Working," "Retirement Benefits and Pensions," and "Health and Diet" for those who have reached the age of 55, as an opportunity for them to rethink their future career plans and the meaning of work. Our post-retirement reemployment rate for FY2023 was 91% (107 out of 117 people).
Expansion of vibrant workplaces for people with disabilities
As well as systematic regular and mid-career hiring, we are taking various steps to enable employees with disabilities to play an active role in a wide range of workplaces, including manufacturing sites and administrative departments. With a focus on work motivation and how well each individual's unique characteristics fit the job description, we determine assignments based on a series of practical workplace training and interviews. We are also taking various measures to fully utilize the potential of employees with disabilities after assignment, such as regular meetings with the employee concerned, follow-up with their workplaces, and other support and consideration led by the Vocational Life Consultants for Persons with Disabilities. In addition, to eliminate obstacles making it difficult for employees with disabilities to work, we are also committed to expanding the number of workplaces available to them through the introduction of barrier-free facilities, support for career development, and initiatives to raise employees' awareness and improve understanding.
Mid-career recruitment
In these times of growing uncertainty, we believe that we need more advanced knowledge, diverse experience, and abilities than ever before in order to solve social issues with speed through our business. For this reason, we are focusing on mid-career recruitment, especially in our priority areas such as DX and research and development. In FY2023, we hired 13 employees in general positions. (Rate of mid-career recruitment: 40.6%)
Human Resource Development
Basic approach
Aichi Steel is committed to developing human resources who can improve their basic skills, which are needed in any environment, and their expertise necessary to adapt to changes, and are able to think and act independently, while practicing the Aichi Way, a set of shared values that must be held by all employees of the Aichi Steel Group whose key words are "Sustain," "Appreciate," and "Create."
Strengthening basic skills and expertise
To strengthen the basic skills required for our operations, Aichi Steel is focusing on three areas: problem-solving capabilities, which are the foundation of work, skills for strong workplace capabilities, and digital literacy, which has been newly added. Our basic approach is to acquire problem-solving capabilities and skills through on-the-job training based on "Genchi-Genbutsu," and to enhance their effectiveness through off-the-job training (group education, training, etc.) We provide digital literacy education mainly through e-Learning, with a menu of educational programs according to the proficiency level of each individual, thereby efficiently improving their skills. In addition, to support self-development efforts, we provide correspondence courses, study assistance, and certification incentive programs to strengthen expertise.
Skill improvement
We conducted PM practical skill training as part of rank-based training to improve employees' specialized knowledge and skills required for execution of operation. In addition, we support skill improvement by providing incentives, training environments, and information for technical skill tests that employees voluntarily take on.
Number of training instructors trained (cumulative)
Number of persons who passed the technical skill test
On-the-job and off-the-job training
We actively and systematically implement on-the-job training, based on the belief that experience and learning through "Genchi-Genbutsu" (on-the-job experience) are essential for human resource development. We have established a system in which each employee reviews their future career plan and regularly discusses with their superior their work assignments and goals for acquiring the skills and knowledge necessary to realize the plan and for developing competencies. Efforts are also made to enhance the effectiveness of our various training programs, such as managers and supervisors instructing junior employees to achieve a synergistic effect between on-the-job and off-the-job training, and top management giving talks on their own experiences to raise participants' motivation.
Digital literacy education
To maintain and improve competitiveness, we recognize that in addition to initiatives at manufacturing sites such as smart factories, we need to promote DX to transform our operations, organization, and corporate culture, and we are working to strengthen the development of our DX human resources. In FY2023, we are speeding up our development of DX leaders by conducting basic digital literacy education, and by determining the DX level of every employee through a DX assessment and using it to build a future education system. We are also working to promote DX companywide by fostering awareness through such events as a Hands-on DX Exhibition and a Generative AI Application Contest.
Efforts to develop human resources for executives
We are engaged in ongoing and systematic training to acquire new management personnel. To increase the self-awareness of the candidates, managing executive officers themselves serve as instructors, and the content focuses on mindset. In addition to equipping them with management and leadership skills that enable them to see and think from a companywide perspective and to create management ideas, we also hone their boldness, vision, sense of speed, and other qualities necessary for assuming higher responsibilities.
Initiatives to Respect Human Rights
Basic approach
Due to the increasing importance of respect for human rights in business globally, plus other factors such as diverse values and globalization of supply chains, there are strong expectations that companies will consider human rights in their corporate activities. To realize a sustainable society, our group will provide value to society and continue to be selected and trusted by society at large. We promote efforts to respect the human rights of all people involved in our corporate activities by dealing with each and every one of our stakeholders with sincerity.
Human rights policy
Through the Aichi Way, which is the Aichi Steel Group's set of common values, and the Aichi Steel Group's Action Guidelines, the Group has always demonstrated the importance of human rights and managed its business in a way that values people. In March 2023, however, we created the Aichi Steel Group's Human Rights Policy with the approval of the Board of Directors to clarify our human rights policy, promote understanding outside the Group, and raise awareness among our employees. In accordance with the United Nations "Guiding Principles on Business and Human Rights," it is positioned as the Aichi Steel Group's highest policy regarding human rights that all officers and employees should comply with. We have also advised all of our business partners, including suppliers, of this policy to gain their understanding and support.
See the following link for the Aichi Steel Group's Human Rights Policy.
Promotion structure
With the General Manager of the Corporate Planning Headquarters in overall charge and the Sustainability Promotion Department as secretariat, the Human Resources Division, General Affairs Division, Purchasing Division, and other related divisions have collaborated to formulate action plans, share initiatives between divisions, and share and discuss social trends regarding human rights. They then report the details of these activities to the Top Management Meeting as appropriate. The Board of Directors monitor and supervise by receiving reports.
Roles of each meeting
Meetings | Composition | Respect for human rights roles |
---|---|---|
Board of Directors | Chair: Chairman Outside Directors (2) Inside Directors (4) |
|
Top Management Meeting | Chair: President Chairman, Executive Vice Presidents In-house Company Presidents, General Managers |
|
Roles of each division
Divisions | Roles |
---|---|
Human Resources Div. |
|
General Affairs Div. |
|
Purchasing Div. |
|
Sustainability Promotion Dept. |
|
Employee awareness and understanding
Aichi Steel is actively promoting awareness-raising and penetration activities to ensure compliance with our human rights policy. As well as conducting human rights education by job level (new hires, career hires, mid-career employees, promoted employees, etc.), we are endeavoring to thoroughly raise awareness through the AICHI STEEL Group Action Guidelines, which specifically set out actions to be taken by all officers and employees of the Group. In FY2024, we will confirm the level of understanding and penetration of compliance among employees through a Compliance Awareness Survey while continuing our awareness-raising activities. At our overseas group companies, we have begun to are undertaking initiatives which include the development and distributedistribution of our human rights policy translated into local languages.
Human Rights Due Diligence
We conduct human rights due diligence to counter human rights risks that may arise in the course of our business activities. In FY2023, as a first step, we implemented a self-check via a self-survey questionnaire for Japanese group companies. We also conducted a desk study of human rights risks using information collected from secondary suppliers and beyond, to identify and assess human rights risks in our Japanese group's major supply chains, including our company's own. In FY2024, we are identifying negative impacts on our company and our Japanese group companies and promoting efforts to prevent and mitigate them. We are also conducting self-evaluation surveys for about 100 primary suppliers of major procurement items to identify key issues that should be prioritized in supply chains.
Consultation contact point
We have introduced an internal whistle-blowing system for the Aichi Steel Group and suppliers in Japan, and have established an in-house consultation contact point for harassment, childcare/nursing care, mental health, and other issues. In addition, we developed new grievance remedy mechanisms, including a human rights consultation contact point available to all stakeholders, both internal and external. In FY2024, we are promoting initiatives such as clarifying the department with jurisdiction over respective consultations and providing information to eligible employees on “JP-MIRAI Assist,” a service which can be used by Toyota Group companies as a consultation contact point for workers from overseas.
Major opportunities for dialogue with stakeholders
Respect for human rights roadmap
Health and Safety
Health
Basic approach
Since its foundation, Aichi Steel has practiced people-oriented management. People-oriented management means realizing "valuable living" and "happiness for employees and their families," with employees leading healthy and active lives both mentally and physically, thereby providing value to society. We position "employee health and safety" as a priority issue, striving to maintain and promote mental and physical health, and promoting the creation of a people-friendly workplace.
Implementation of health and productivity management
Aichi Steel believes that efforts to maintain and improve employee health bring a range of benefits, including vitality and productivity improvements for the organization. Based on this belief, we are committed to implementing health and productivity management for sustainable growth. In our Medium-term Management Plan, we have established quantitative targets for health, and are working on continuous improvement through a PDCA cycle. With mental health and the prevention of lifestyle-related diseases as our priority issues, we are working to enhance various measures by promoting collaborative health*, a cooperative effort among the company, health insurance society, and labor union. In recognition of these initiatives, we were recognized for the seventh consecutive year in 2024 as a Certified Health & Productivity Management Outstanding Organization.
- Efficient and effective implementation of disease prevention and health promotion for insured individuals through active collaboration between the insurer and the business with clearly assigned roles and favorable workplace environments
Organization chart
Prevention of lifestyle-related diseases
With the aim of improving lifestyle habits for better health, Aichi Steel is promoting its "Health Challenge 8" initiative to raise employees' health awareness and encourage behavioral changes. We are addressing health promotion by devising ways for employees and workplaces to proactively enjoy practicing healthy habits, such as by holding inter-workplace events aimed at creating habits related to eight items: bodyweight, breakfast, alcohol consumption, snacking between meals, smoking, exercise, sleep, and stress. We have also made a companywide effort to prohibit smoking, and in 2024, on World No Tobacco Day (May 31), we launched a ban on smoking on all company premises.
Mental health
Aichi Steel is working to prevent the occurrence of mental health issues and ensure their early detection and care by establishing a Mental Health Consulting Counter, providing education to both regular employees and supervisors, and providing consultations with a medical adviser on mental health for employees with mental health issues. In addition, we conduct stress checks once a year for all employees, and promote mental health by providing care for high-stress individuals and high-risk workplaces.
Harassment
This is not only an assault on personal dignity and a disturbance in the workplace, but also a problem that severely impacts business management. This is why labor and management are working together to create harassment-free workplaces. We have established the Aichi Steel Harassment Prevention Guidelines, which stipulate measures for preventing harassment and other matters for the company and employees to observe, and provide education to all executive officers and employees. We have also established dedicated consultation contact points internally and externally to address harassment issues, and we are allocating consultants in each workplace to systematically suppress harassment while achieving early detection and resolution. In FY2023, we received 15 consultation requests and reports. These are promptly examined and fact-checked by the Investigative Committee, which is comprised of members from both labor and management, and efforts are made to prevent recurrence, including strict action and education for supervisors. In addition, workplace counselors themselves raise awareness of harassment by regularly publishing "Counselor News" on the subject and distributing it to all employees, and by providing education on harassment to all employees.
Organization chart
Safety
Basic approach
The Aichi Steel Group recognizes that safety takes priority over all. In accordance with our Basic Philosophy for Safety and Health, we aim to create a safe and secure work environment for everyone working on our premises, and to transform into a company with a safety culture.
Basic Philosophy for Safety and Health
Safe work, Reliable work, Skilled work. Safe work is "the gate" to all work. Let us pass through this gate.
Promotion structure
Recognizing that safety and quality are the foundation for creating added value, we promote companywide activities with the Risk Management Headquarters as the overall driving force. The Safety, Health & Environment Division plays a central role in safety, and based on the belief that all accidents and injuries can be eliminated, it strives to create a safe and healthy work environment for all employees on our premises by sharing companywide policies with our in-house companies, headquarters, Group companies, and cooperating companies.
Promotion structure chart
Activity policy
To prevent accidents, the Aichi Steel Group is developing safety activities based on the three pillars of safety management, fundamentally safe designs, and the development of safety-conscious human resources.
Fiscal 2023 initiatives
Safety management
Recurrence prevention activities
Whenever there is an internal or external disaster that could potentially occur in other workplaces, we issue a Disaster, Fire, and Near-miss Cross-Division Deployment Sheet to try to prevent a recurrence.
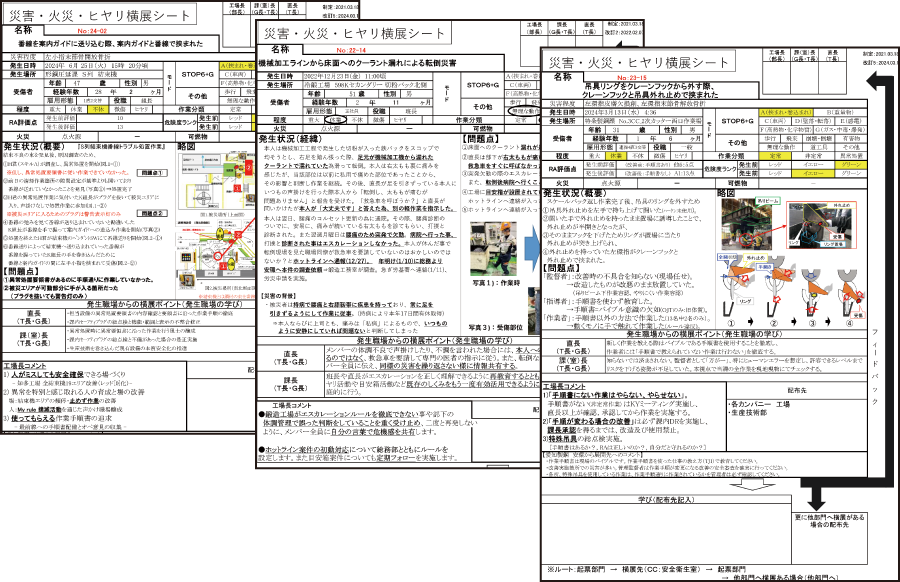
Prevention activities
For safer implementation of high-risk operations identified in risk assessments, we promote prevention activities by making improvements and conducting safety reviews.
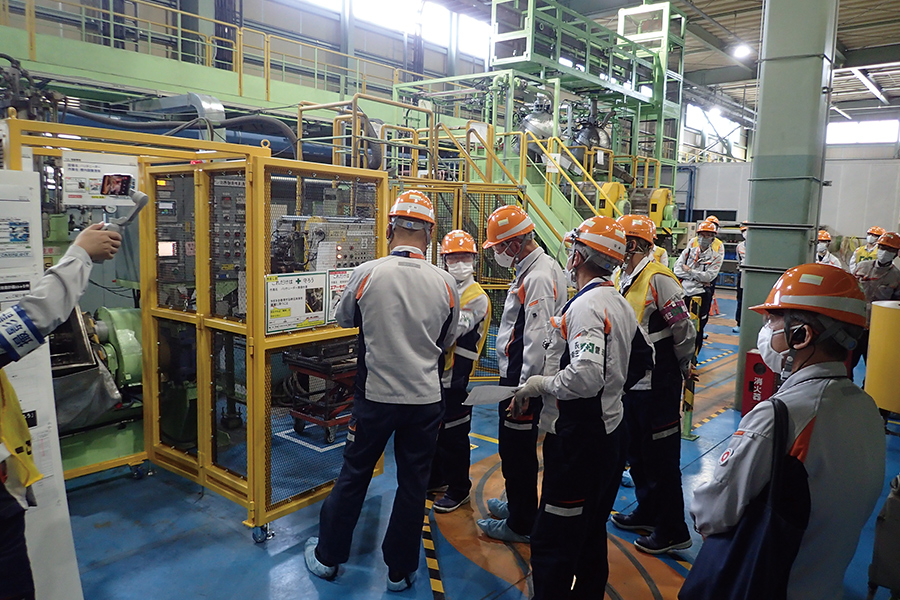
Fundamentally safe designs
Management Safety Inspection Meeting
This initiative promotes the horizontal implementation of safety-related initiatives through guidance on and sharing of measures to eliminate hazardous sources specific to the workplace based on onsite inspections by top management.
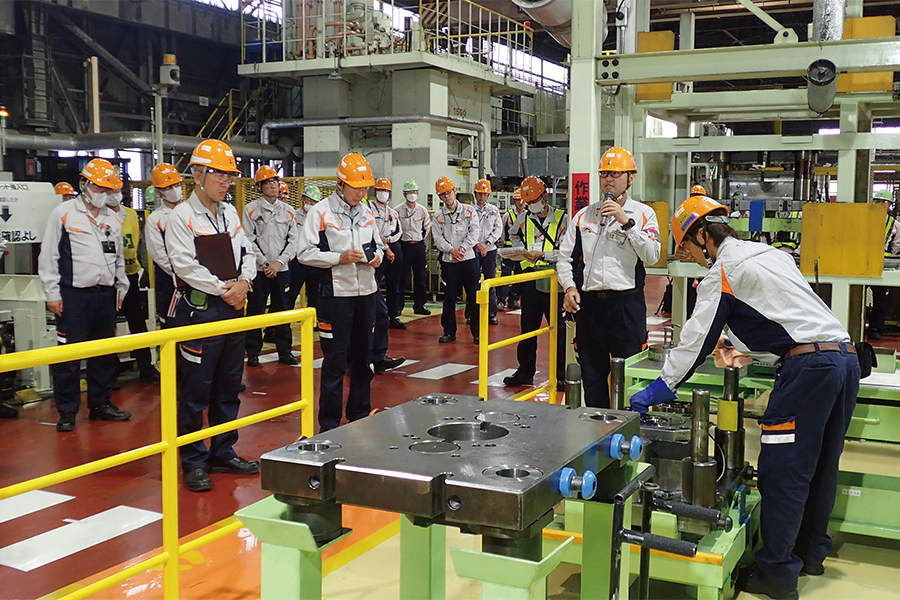
Learning and sharing past accidents
This initiative aims to prevent the recurrence of accidents by making sure that measures to prevent past accidents are being maintained and continued.
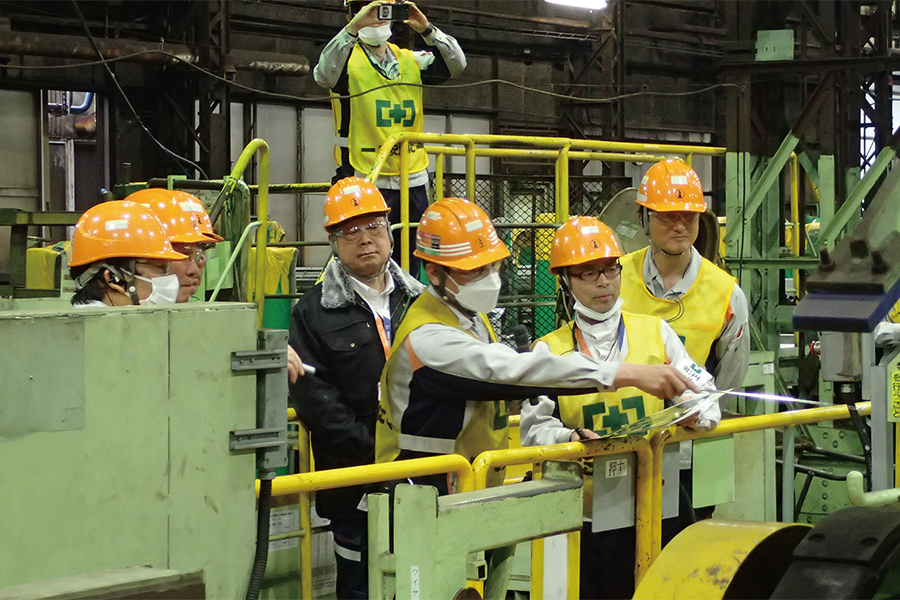
Developing safety-conscious human resources
Training people in charge of safety
We are working to raise the level of our company's safety and health management, developing highly safety-conscious personnel by giving the foremen responsible for on-site safety two months of classroom learning about health and safety and practical on-site training in safety diagnosis skills.
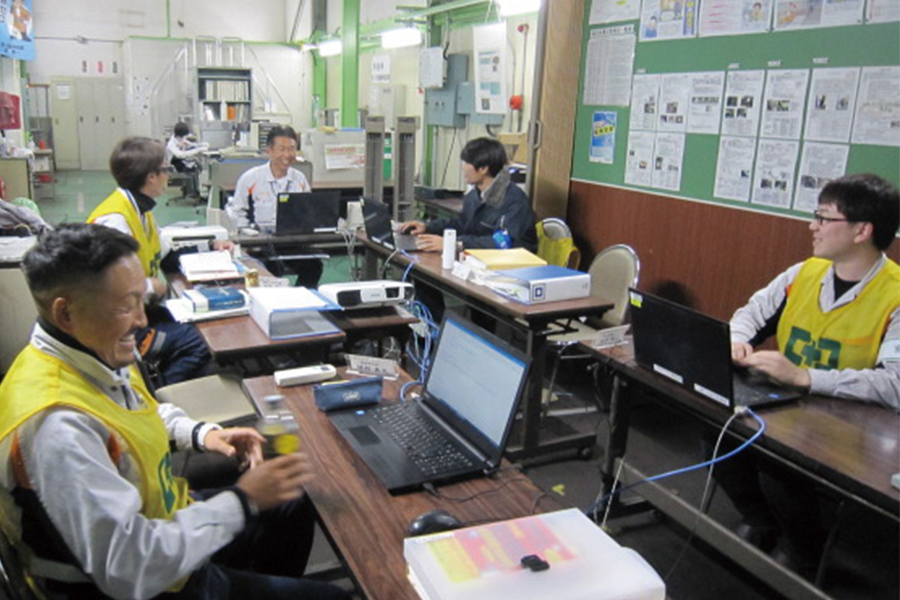
Skill competition
This competition is designed to raise the level of our daily safety awareness and skill training by confirming and improving this level through competition.
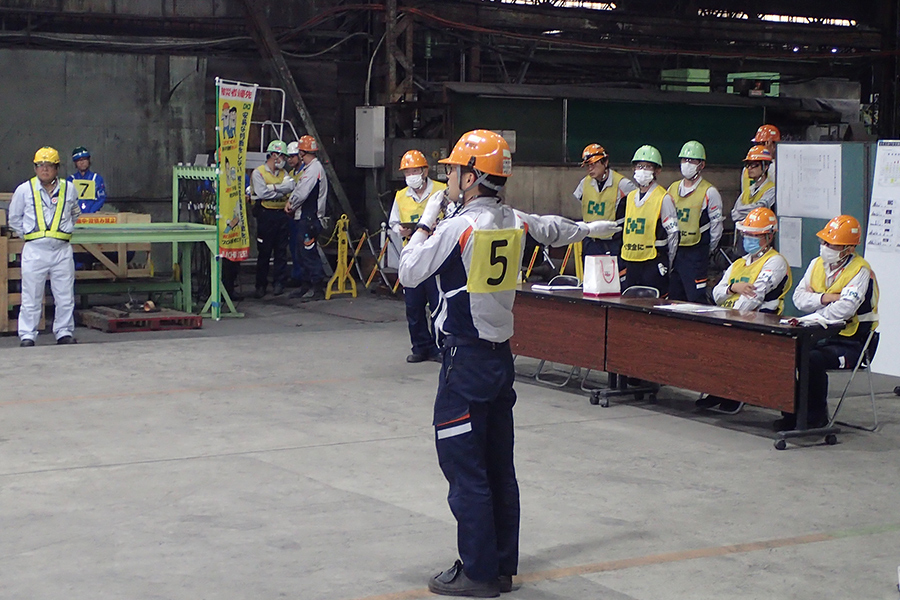
Prevention of occupational accidents
We conduct risk assessments aimed at eliminating occupational accidents. Especially for high-risk work that could lead to significant or serious accidents, we strive to prevent accidents by systematically implementing improvements through fundamentally safety measures that eliminate the causes and reduce the risks. For all occupational accidents, we work to prevent recurrence by clarifying the true cause, including the context, and informing the group and cooperating companies of the accident.
Number of lost time accidents and lost time frequency rate
Research and Development
Basic approach
To achieve the Vision 2030 management guideline of "Creation of a prosperous society through business reform," Aichi Steel believes that conducting research and development in line with our business strategy, and helping to address social issues by reforming existing businesses and creating new businesses, will lead to sustainable growth for the company. For this reason, we have formulated the 2030 Development Vision and established a research and development policy, as well as promoting the effective use of intellectual property.
Areas of contribution through research and development
Our 2030 Development Vision was formulated to solve social issues through our business, and defines the priority areas as "autonomous driving," "vehicle electrification," "food," and "health and safety," with a focus on the development of next-generation mobility and products that enrich people's lives. By creating new highly functional products, we will contribute to the realization of a sustainable smart society.
Strengths of "integrated forging with steel making" and "material manufacturer"
Aichi Steel utilizes the strengths of its integrated forging with steel making processes, in which a wide variety of components are added to raw steel scrap to create specialty steel with properties and functions such as strength and heat resistance, and then finished into forged products, and the knowledge it has accumulated as a materials manufacturer since its founding, to develop products that address to changes in society and meet the needs of society.
Development based on integrating forging with steel making processes
Expansion of technology as a materials manufacturer
Launch of companywide cross-sectional standardization activities
Standardization activities to establish standards and specifications for new products and technologies are essential for ensuring quality and reliability, returning the fruits of research and development to wider society, and ensuring competitiveness in global business. In FY2023, we established the Standardization Promotion Committee, a companywide, cross-sectional organization. In FY2024, the committee is active in the electric furnace industry, reporting and discussing the status of activities, including environmentally friendly electric furnace steel materials, and making plans for the future.
Standardization promotion structure
Our Standardization Promotion Committee is chaired by our head of R&D, the General Manager of the Research and Development Headquarters, who serves as CSO (Chief Standardization Offcer) and oversees standardization, R&D, and intellectual property in an integrated manner. The general manager of each in-house company's business headquarters and the general manager of each development division are also placed in charge of divisions to ensure alignment with business strategies. A representative manager of each division that conducts standardization activities is appointed as a divisional committee member. Led by this committee, we carry out strategic standardization activities throughout the whole company, while focusing on raising in-house awareness and training personnel for standardization.
Standardization promotion structure chart
Intellectual Property
Basic approach
Aichi Steel has established proactive intellectual property (business expansion and challenges), defensive intellectual property (business stability), and basic activities (human resource development and structure building) as its priority policies, setting targets for each and working to promote intellectual property activities that lead to steady growth.
Promotion structure
Aichi Steel has established an Intellectual Property Committee to promote intellectual property activities. The committee is chaired by the Research and Development Headquarters general manager, with general managers of each in-house company, headquarters, and technology division as members.
Intellectual Property Committee
Increase in new business patents and strengthening of patent system
The number of our related patents has increased in recent years as we have stepped up development in new business areas.Besides the conventional protection of intellectual property, our development and intellectual property divisions have strengthened their cooperation and established a system geared toward strategic patent applications that lead to the creation of new value, thereby improving the quality of our patents. We will continue to promote activities aimed at building a patent portfolio that will help us maintain and improve the competitive advantage of our business and expand new business.
Changes in the number of patents held
New Business Field Development Initiatives
Autonomous driving enabled by GMPS
Aichi Steel is working toward the early commercialization of our Global Magnetic Positioning System (GMPS), an autonomous driving support system that uses our proprietary magneto-impedance (MI) sensors to detect magnetic markers placed on roads, enabling the estimation of automotive positions with high accuracy on the millimeter scale even in harsh environments. Since 2017, we have conducted more than 30 verification trials in various locations and environments with national and local governments, private companies, and organizations, and have received high ratings in terms of performance and reliability.In 2022, GMPS was adopted for use in an autonomous driving bus operating between Yanaizu Station and Rikuzen-Yokoyama Station on JR East's Kesennuma Line bus rapid transit (BRT). In 2023, it was on track to be put into practical use as an automated traction vehicle on factory premises. We have taken this opportunity to add the on-site logistics market to our focus areas, and are promoting commercialization of GMPS. Utilizing our advanced technical capabilities that have achieved things such as ultra-sensitive MI sensors, high-quality, low-cost, low magnetic-force markers, and our own magnetic field noise elimination system, we are contributing to building a safe and secure mobility society.
Development of materials and parts for next-generation electric axles
To address the growing demand for electric axles accompanying the electrification of automobiles and the risks of resources such as rare earths, we are developing materials and components for motors and reduction gears that will help make electric axles smaller, lighter, and more resource-efficient. We are the first company in the world to successfully verify the technology of a next-generation electric axle with high-speed rotation and high speed reduction by combining a compact, lightweight motor capable of 34,000 rpm and a compact, high reduction gearbox.Utilizing elemental and evaluation technologies obtained as a result of these efforts, such as material design and steel processes, we are promoting the development and commercialization of increasingly high functional parts and materials.
Quality and Production
Basic approach
We have formulated a Quality Control Basic Policy as part of our efforts to promote quality assurance initiatives.
Aichi Steel has always focused on the manufacturing capabilities of integrated forging with steel making processes, which cover everything from material design to production of steel, forged products, and electronic components. We have continued to provide our customers with highly functional and high-quality materials and parts with high strength, durability, and machinability, which are indispensable in the automotive and other industries. This stable supply of high-quality, low-cost products has been supported by the implementation of quality management and the evolution of manufacturing capabilities through the Toyota Production System (TPS), Total Quality Management (TQM), and Total Productive Maintenance (TPM). Using this as a foundation, we are working to build production systems that are resilient to changes as we face increasing uncertainty, including geopolitical risks and sharp price fluctuations.
We have formulated a Quality Control Basic Policy as part of our efforts to promote quality assurance initiatives.
TPS activities
Aichi Steel is striving to improve its lean manufacturing capabilities by promoting cost reduction through thorough elimination of waste based on the two pillars of TPS: just in time and automation. The in-house companies systematically address improvement themes for cost reduction identified from the perspective of TPS, and their results are shared companywide through a TPS convention held at the end of the fiscal year.
We have established a TPS trainee system to implement TPS, where we focus on human resource development. We train personnel selected as TPS promotion leaders through classroom lectures as well as practical learning, including case studies, in order to effectively apply TPS methods in the workplace. Also, to facilitate the smooth introduction of TPS to our production sites, we are promoting the acquisition of TPS methods appropriate to the role of each employee by providing a wider range of level-based training. With these two activities, cost reduction and human resource development, we are building flexible production systems that are resilient to change.
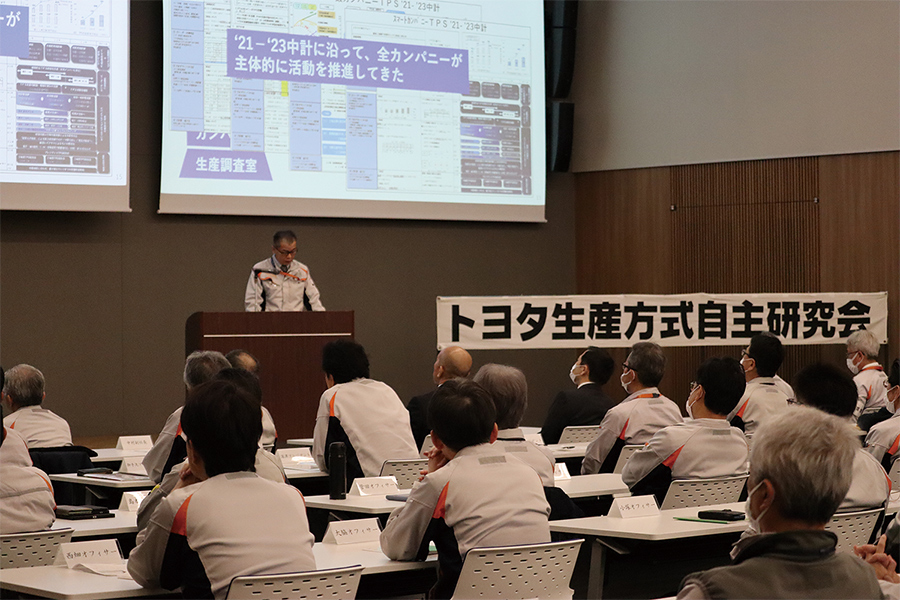
Improvement themes
Topics | Composition |
---|---|
Labor-saving | Improvement of single-person productivity per day, consolidation of equipment |
Shortening of lead time | Reduction of production quantity, streamlining of production |
Enhancement of production potential | Reduction of downtime, improvement of specific consumption |
Reduction of man-hours | Reduction of downtime, shortening of MCT* |
- Time required to machine and assemble a single part (Machine Cycle Time)
TQM activities
Implementation of quality management based on TQM
Based on the fundamental TQM principles of "customer first," "full participation," and "constant improvement," the Aichi Steel Group is engaged in TQM activities to implement quality management. This is done by "improving the quality of products and work" and "increasing the vitality of people and the organization."
Deployment of TQM activities
"Jikotei Kanketsu" with customer first
Based on the concept that quality is built in the process, which was born from Toyota Motor Corporation's manufacturing site, Aichi Steel is promoting "Jikotei Kanketsu" activities to ensure that no defective products are passed on to customers, including those in back-end processes, and that products are always delivered on time to satisfy customers. In addition to manufacturing sites, we are also expanding our activities to our administrative divisions with the aim of strengthening our competitiveness.
QC circle activities with full participation
Aichi Steel is working to establish and expand our QC circle activities as a means of improving operations in workplaces. We are working to develop human resources and revitalize our organization through consistent team efforts to identify problems, clarify issues, and formulate and implement countermeasures. In FY2023, 167 circles conducted activities, and 14 cases received external awards. For ingenuity and creativity proposal activities by individuals*, we set a target of at least one proposal per month, and all eligible employees achieved the target throughout the year. As a result of these efforts, in FY2023 we received three awards from the Minister of Education, Culture, Sports, Science and Technology.
- Activities to encourage and evaluate employees' suggestions on how to improve the efficiency and quality of daily operations. Rewards are given based on the size of the effect, the number of proposals per year, and other factors in order to increase employees' motivation.
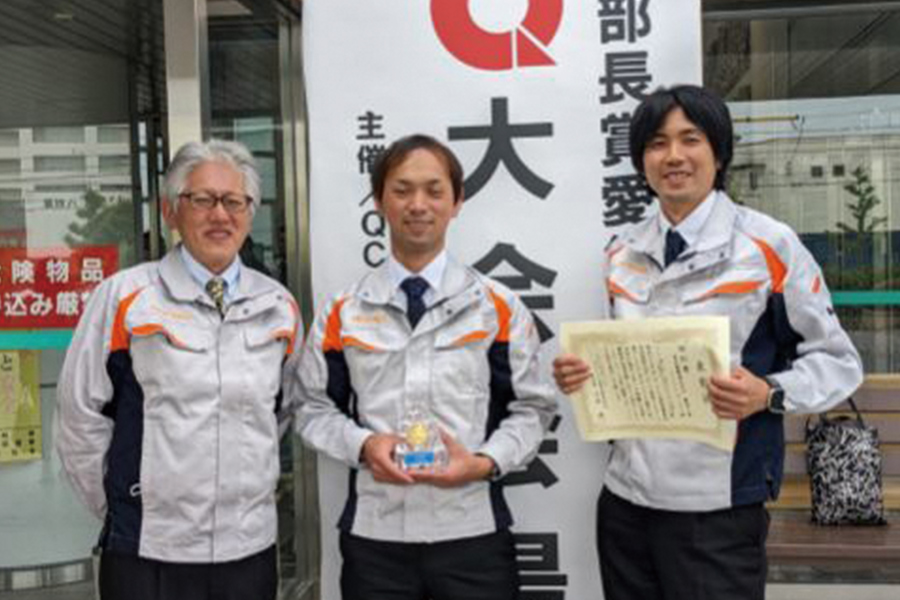
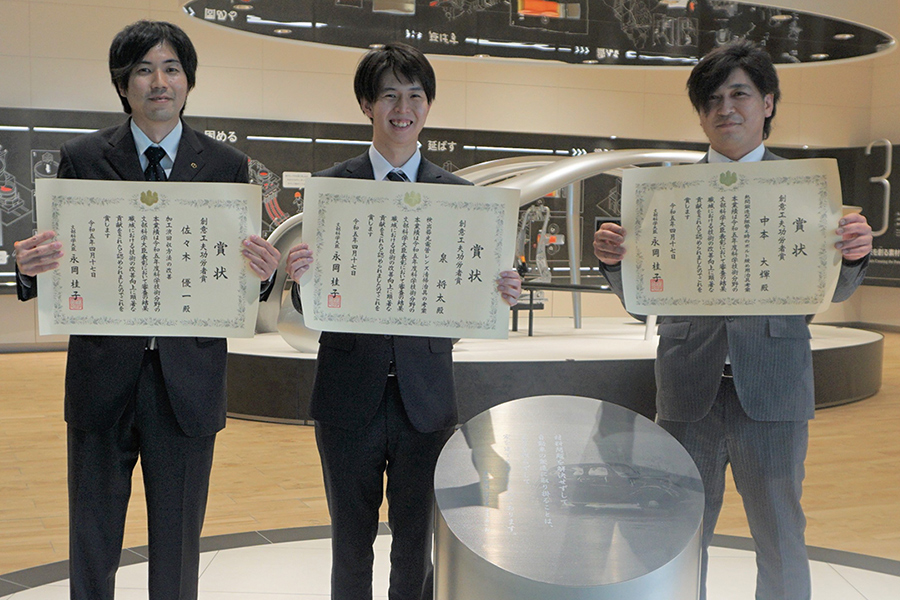
To consistently meet quality requirements
The automotive industry is undergoing a once-in-a-century transformation, and its quality requirements are also changing. We are always trying to maintain and strengthen our competitiveness by delivering the level of quality that is required. One of our efforts in this regard is to nurture expert personnel who have the ability to utilize technologies such as IoT, big data, and AI. Utilizing the Toyota Group Machine Learning Practice Dojo venue, we enhance the learning effect by using specific improvement themes as the subject matter, such as "automation of rear shaft visual inspection," and verifying the process from improvement to measurement of results in a practical setting.
TPM activities
We are committed to TPM activities to ensure effcient production of high-quality products. Based on the three key concepts of "full participation," "initial cleanup," and "HR with strong technical capabilities," we aim to transform people's behavior and on-site facilities to achieve zero breakdowns and zero defects by analyzing, addressing, and improving production facilities before breakdowns occur.
With operator self-maintenance as the most important activity, we have set quantitative targets for activities such as three zeros in equipment failure, quality defects, and occupational accidents, and productivity improvement through the reduction of production losses.
In FY2023, we have achieved steady results, with 268 employees having acquired level 1 (top grade) self-maintenance personnel certification (acquisition rate: 20.5%) and a 31.5% reduction in total facility failures (compared to FY2021.) To further promote and strengthen our TPM activities, we will work on improving quality and maintaining an efficient production system, such as by using DX for data analysis and visualization.
Fostering an awareness and culture of quality
The out-of-tolerance steel length problem identified in FY2023 prompted all management and employees to go back to our founding principles and launch activities to ensure that quality problems are never repeated.
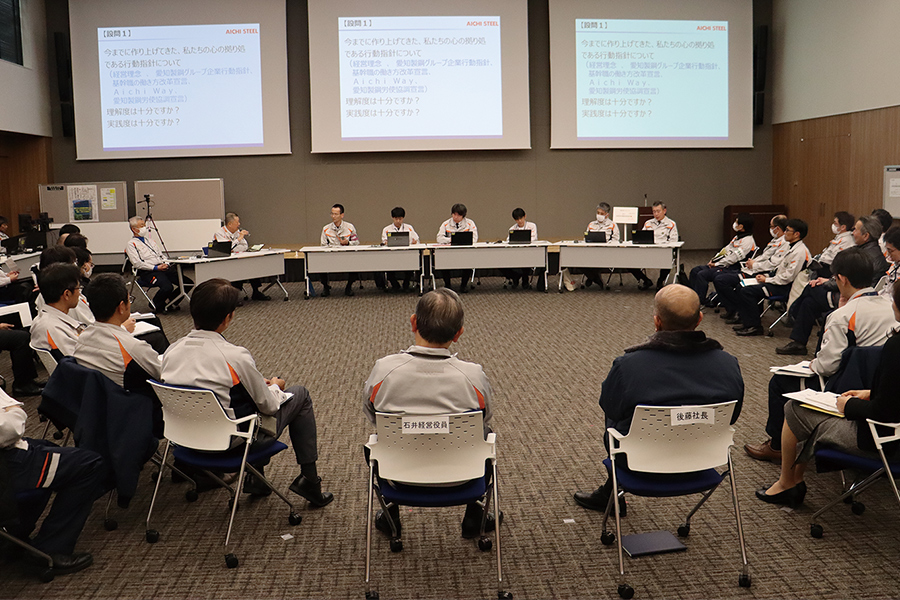
Activity Category | Implementation Item | Details |
---|---|---|
Human resource development (awareness reform) | Dialogue meetings | Management and employees share and discuss thoughts and values |
Quality restart day | Activity to prevent people from forgetting the lessons learned | |
Special exhibitions | Informing all employees of the circumstances of the outbreak and lessons learned from the problem | |
Fostering a workplace culture | Workplace group discussions | Discussions in each workplace on what should be done to prevent recurrence |
Revision of Aichi Steel Group's Action Guidelines | Opportunity for everyone to reaffirm and relearn the essence of compliance and our responsibilities as a company | |
Inner branding | Reaffirming our corporate philosophy and values for the entire company to work together to perform well and improve quality | |
Strengthening mechanisms and organization | Establishment of Risk Management Headquarters | Strengthening and enforcing compliance and governance companywide |
Whistle-blowing system | Improving availability and convenience, expanding external consultation services, conducting public awareness activities |
Stakeholder relations
Basic approach
Aichi Steel conducts its business activities through relationships with various stakeholders, so building positive relationships with those stakeholders is important for improving our corporate value. Through proactive dialogue with stakeholders, we are able to incorporate the needs of society and expectations for us into our business activities, and encourage them to feel a sense of closeness with Aichi Steel. In this way, we are able to grow alongside all of our stakeholders, including customers, shareholders and investors, employees, suppliers, and local communities.
Stakeholders | Initiatives to promote dialogue | FY2023 results |
---|---|---|
Customers |
|
Number of inquiries 1,225
|
Shareholders and investors |
|
Number of dialogues with
institutional investors (total) 45 |
Employees |
|
Number of labor-management
roundtables and conferences 19 |
Suppliers |
|
Number of
participating companies 125 |
Local communities |
|
Employee participation rate
in social contribution activities 78% |
Promotion of dialogue with employees
To provide value to society and achieve sustainable growth, it is essential for Aichi Steel to ensure a high level of employee engagement, which is the source of value creation. We are promoting initiatives to increase employee engagement by building dialogues with our employees, creating comfortable workplaces, and improving our personnel system. In 2020, the 80th anniversary of our founding, we signed the Declaration on Labor-management Cooperation, in which labor and management mutually confirm and share the goal of overcoming any difficulties through mutual trust between labor and management and aiming for a company full of smiles with everyone involved. In addition, labor-management meetings were reviewed and new labor-management roundtables at the in-house company and headquarters levels were held twice, to allow the two parties to more frankly exchange opinions and accelerate reform.
We are making efforts to have labor and management honestly exchange opinions, deepen understanding, and cooperate with each other on familiar issues and countermeasures at the in-house company and headquarters levels. In FY2023, we increased subsidies for workplace trips and get-togethers in order to revitalize workplace communication, which had been somewhat lacking since the COVID-19 pandemic. To create open workplaces where diversity is respected and everyone can work comfortably, we have also focused on improving workplace environments by conducting a morale survey of all employees, improving rest areas at workplaces, constructing a multi-story parking garage, and rebuilding our dormitory for single employees.
Initiatives to improve engagement
Aichi Steel conducts an annual engagement survey of all employees. Based on the results of the analysis from various perspectives, such as motivation toward work, sense of growth through work, support from superiors, and workplace culture, we are working to develop various personnel measures and improve management in each workplace. In addition, managers are working to improve their management skills such as by attending expert lectures and annual leadership courses. In FY2023, we revamped the survey with the goal of deepening our analysis and clarifying issues for each workplace. Going forward, we will continue by incorporating our responses to emerging issues into a newly launched leadership training program, and by confirming improvements to our workplace culture and the results of our efforts.
Changes in engagement evaluation
Strengthening partnerships with suppliers
Superior raw materials, parts, and technologies supplied by our suppliers are essential for manufacturing Aichi Steel's products. Based on our belief that collaboration with suppliers is important in addressing various sustainability issues, we are working to build a relationship of trust with them through close communication, and to establish and strengthen a sustainable supply chain that allows us to grow together and share our achievements.
Every year in April, Aichi Steel holds the Hokokai* General Meeting to explain the business environment and company policies and share information on initiatives and goals regarding safety, compliance, and sustainability. In FY2023, we established our Supplier Sustainability Guidelines, which specify in more detail the actions expected of our suppliers, and we require them to conduct activities based on these guidelines. The guidelines were distributed at the Hokokai General Meeting to all 125 companies to inform them and encourage their cooperation. We also provide support activities to each company by offering advice on safety, quality, and other issues according to their circumstances, and engage in improvement activities throughout the supply chain, such as mutual improvement through improvement case study meetings and the VA Exhibition as well as the horizontal development of good practices.
- An organization consisting of suppliers aiming for mutual development based on partnership and mutual trust with Aichi Steel
Enhancement of supply chain resilience
Amidst rising geopolitical risks in addition to natural disasters and accidents, Aichi Steel is focusing on the stable procurement of raw materials and resources. By gaining information on the location, source of materials, and processes of our suppliers' manufacturing sites and quantifying the risks, we are taking necessary measures such as multi-sourcing and securing of inventories, while building structures that enable prompt initial response and recovery actions.
Strengthening relationships with local communities
As a good corporate citizen, we recognize the importance of communicating with local communities through social contribution activities and so on, and are engaged with them in co-creation activities. Specifically, we are developing activities based on the four pillars: clean, green, creative, and volunteer support. Such activities not only strengthen our relationships with local communities, but also help develop a social issue solving mindset among employees and provide feedback on our business activities. We will continue working actively toward the realization of a sustainable local community, to which every one of our employees can make a contribution.
4 pillars | Main Activities |
---|---|
Clean |
|
Green |
|
Creative |
|
Volunteer support |
|